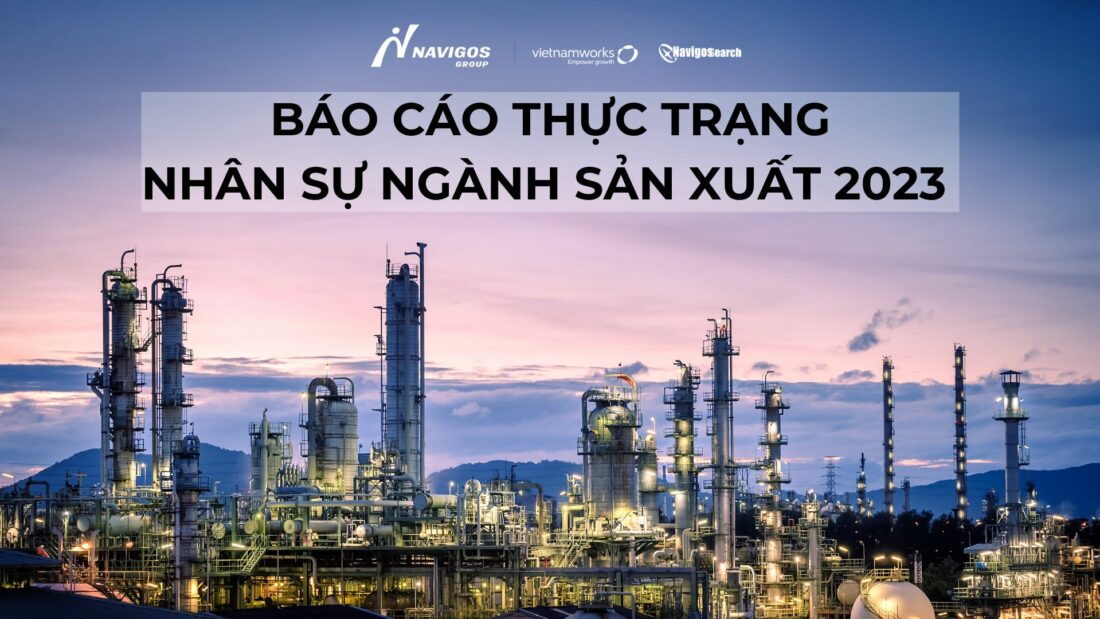
Report On Human Resources Status Of The Manufacturing Industry In 2023
2 yearsago 0 Comments 1.6k Views
Navigos Group releases the Human Resources Status Report of the Manufacturing Industry in 2023 to provide an overview on the Manufacturing market and the improvisation solutions of Companies and Employees.
Ho Chi Minh City, August 4, 2023 – Navigos Group releases the Human Resources Status Report of the Manufacturing Industry in 2023 to provide an overview on the Manufacturing market and the improvisation solutions of Companies and Employees. The report is conducted from a survey of more than 1000 Employees and 500 Companies in the Manufacturing market, including: High-Tech industry; Textile / Footwear industry; Pharmaceuticals / Biotechnology industry; Agriculture / Forestry industry; Industrial Product industry; Consumer Goods / Food industry; Production of Construction Materials industry; Automotive / Automotive industry; and other industries.
PART 1: THE CURRENT SITUATION OF THE MANUFACTURING INDUSTRY IN THIS ECONOMIC RECESSION
I. FOR COMPANIES
1. Revenue decreased by industries
At least 50% of Companies face a decrease in revenue in each industry, in which the most affected industry is up to 91% of enterprises.
According to collected data, more than 50% of enterprises in each industry recorded a decrease from less than 10% to over 40% of total revenue in the context of the economic downturn. Besides, there are still at least 9%, and at most 50% of enterprises in all industries that have recorded revenue unchanged, have not been affected or are continuing to grow.
In detail:
-
The High-Tech industry accounts for 28% of corporate growth and 21% of revenue decline (less than 10%).
-
44% of companies in the Textile / Footwear industry have experienced a 20% – 40% decrease in revenue, while only 8% of companies experienced growth.
-
37% of company revenue in the Pharmaceuticals / Biotechnology industry has decreased to below 20%, while 21% of business continues to grow.
-
42% of companies in the Agriculture / Forestry industry have maintained growth and have not been significantly affected.
-
22% of companies in the Industrial Product industry have decreased to below 20%, while 9% of enterprises have grown.
-
26% of companies in the Consumer Goods / Food industry have witnessed their revenue drop below 20%, while 21% have not been affected.
-
91% of companies in the Production of Construction Materials industry experienced a decrease in revenue.
-
The Automotive / Automotive industry also faces difficulties, with 30% of companies experiencing a decrease in revenue of over 40%.
-
The impact of other industries is greater, with 33% of companies’ revenue falling to over 40%.
For more details please refer to the report
2. Factors that affect the revenue of industries in the market
The decrease in revenue of the Companies is largely affected by both domestic and foreign demand factors at the same time.
On revenue-affecting factors, at least 33% of companies in most of the surveyed industries recorded a simultaneous influence from both domestic and foreign demand. However, the effects of both factors vary differently across different industries.
In detail:
-
The High-Tech industry accounts for 28% of corporate growth and 21% of revenue decline (less than 10%).
-
44% of companies in the Textile / Footwear industry have experienced a 20%–40% decrease in revenue, while only 8% of companies experienced growth.
-
37% of company revenue in the Pharmaceuticals / Biotechnology industry has decreased to below 20%, while 21% of business continues to grow.
-
42% of companies in the Agriculture / Forestry industry have maintained growth and have not been significantly affected.
-
22% of companies in the Industrial Product industry have decreased to below 20%, while 9% of enterprises have grown.
-
26% of companies in the Consumer Goods / Food industry have witnessed their revenue drop below 20%, while 21% have not been affected.
-
91% of companies in the Production of Construction Materials industry experienced a decrease in revenue.
-
The Automotive / Automotive industry also faces difficulties, with 30% of companies experiencing a decrease in revenue of over 40%.
-
The impact of other industries is greater, with 33% of companies’ revenue falling to over 40%.
For more details please refer to the report
3. The Adaptive Solutions of Companies
3.1 The Adaptive Solutions
Maintaining scale or scaling down are the two top solutions chosen by Companies to improvise in the context of the economic downturn.
On average, 41% of companies in each industry say that their priority is maintaining the current scale. On the other hand, an average of 30% of other companies choose to downsize.
However, about 7-25% of companies in each industry claim that they would expand their scale, and under 36% of the rest would receive orders to process other products. This highlights that businesses are still making effort to improvise and maintain their operations amidst the gloomy economic landscape.
In detail:
-
The High-tech industry responds by receiving more orders and reducing scale (both at 31%).
-
The Textiles / Footwear industry chooses to maintain its current scale (41% of companies), but 32% of companies choose to downsize.
-
The Pharmaceuticals / Biotechnology industry is also attempting to maintain its current scale (43%), with 36% of companies choosing to produce other products.
-
42% of companies in the Agriculture / Forestry industry maintain their scale.
-
In the Industrial Product industry, 47% of companies choose to maintain their scale.
-
43% of companies in the Consumer Goods / Food industry choose to maintain business scale.
-
38% of companies in the Production of Construction Materials industry choose to maintain their scale, while 31% choose to reduce their scale.
-
In the Automation / Automotive industry, 52% of companies are able to maintain business scale.
-
In other industries, 42% of companies maintain scale and 42% of them choose to reduce scale.
For more details please refer to the report
3.2 Solutions for reducing scale
Companies prioritize reducing working hours and reducing labor for the purpose of downsizing.
Reducing working hours and cutting labor are the two dominant choices among an average of 38-38.5% of companies in each industry. Following that, about 4-33% of companies reduce production lines, and lastly, only about under 9% of companies choose to close down their factories.
In detail:
-
In the High-tech industry, 56% of companies choose to downsize through layoffs.
-
In the Textile / Footwear industry, 52% of companies choose to reduce their working hours..
-
The Pharmaceuticals / Biotechnology industry has up to 50% of businesses choosing the solution to reduce working hours.
-
The Agriculture / Forestry industry has 38% of companies cutting labor and 33% of companies choosing to reduce working hours.
-
In the Industrial Products industry, 46% of companies choose to reduce working hours.
-
The Consumer Goods / Food industry has 42% of businesses reducing working hours and 38% reducing labor.
-
In the Production of Construction Materials industry, 38% of companies choose to reduce working hours and 34% choose to reduce labor.
-
The Automation / Automotive industry has up to 52% of companies reducing labor
-
In other industries, 42% of companies decided to lay off employees to maintain business.
For more details please refer to the report
3.3 The percentage of workforce reduction
The majority of surveyed Companies laid off less than 10% employees.
For the personnel-reducing solution, most companies in the survey (at least 59%) cut less than 10% of their workforce. “10-20% cut” was the 2nd highest choice with a rate of less than 30% per industry. It is followed by the choice of “20 – 40% cut, which accounts for under 20% per industry. Lastly, only 4 industries have companies (less than 10%) that had to cut their workforce by more than 40%.
For more details please refer to the report
II. FOR EMPLOYEES
1. Salary reduction
Most workers in the manufacturing industry face a 30-50% salary reduction.
According to statistics, 58% of manufacturing employees had their total salary reduced by 30 – 50%, 34% of manufacturing employees had their total salary reduced by less than 10%; and 6% of employees had their total salary reduced by 10 – 30%. Only 2% of participants had over 50% total salary reduced.
Besides, they also had their working hours reduced, overtime pay reduced and did not receive the usual allowances or benefits.
2. Improvising solutions to difficult situation & Skills to be honed
Most employees choose to cut living costs and enhance skills to cope with difficulties.
60% of surveyed employees choose to cut living costs to cope with difficulties, 37% work outside and only 3% choose to work more overtime to increase income.
In addition, surveyed employees share that they should also enhance soft and hard skills to maintain competitive advantages. The majority of respondents choose to improve their management skills (39%), financial management skills (29%) and technology application skills in production (24%).
3. Employees’ expectations towards Companies
Employees expect to maintain their salary, allowances/benefits and guarantee long-term contracts.
During the current period, 35% of employees hope to avoid salary reduction, 28% of them expect to receive long-term contract protection, 28% expect to maintain benefits, and 9% expect to receive sufficient working hours.
PART 2: EXPECTATION FOR ECONOMIC RECOVERY
I. COMPANIES PREDICTION ABOUT RECOVERY TIME
Most Companies predict that it will take 12 months or more for the market to recover.
Most companies (39%) expect the market to take 12 months or even longer to recover. Only 8% of respondents believe that the economy will recover in three months.
Therefore, from the overall market situation, it is shown that companies expect business recovery will not occur soon. Recognizing this comprehensive circumstance, companies will therefore have the foundation to put forward more appropriate countermeasures.
II. LOOK FORWARD TO THE GOVERNMENT’S SUPPORT
Policies to reduce taxes, fees and reduce loan interest rates are the top expectations of Companies.
Figures from the report show that 29-70% of companies expect to be supported by the government in terms of tax and fee reduction. Apart from that, 7-50% of companies expect support from policies that reduce loan interest rates. The remaining few companies want to simplify administrative procedures, reduce land rent, and other expectations.
In detail:
-
In the High-tech industry, companies mainly expect to reduce fees and charges (70%).
-
In the Textile / Footwear industry, 56% of companies expect the government to reduce fees and charges.
-
The Pharmaceuticals / Biotechnology industry stands out, with 50% of companies expecting to reduce loan interest rates.
-
The Agriculture / Forestry industry has 34% of companies that expect to reduce loan interest rates.
-
The remaining industries such as Industrial Products, Consumer Goods / Food, Production of Construction Materials, Automation / Automotive and others, mostly expect to reduce fees and charges.
For more details please refer to the report
III. COMPANY STRATEGIES
Most companies (62%) still choose the solution to take advantage of the current situation to improve productivity and stay ahead of the market. Only 38% of companies focus on maintaining minimal company operations.
1. Company strategies – Looking at each industry
Companies focus on improving productivity in order to stay ahead of the post-crisis market, in addition to ensuring minimum business operations.
Surveyed companies basically implement two strategies to cope with the current difficult period. It takes time to implement productivity solutions to stay ahead of the post-crisis market or ensure minimal business operations. In particular, the strategy of “Prepare for the market” is most prominent when it is actively implemented by the majority of companies in all industries.
In detail:
-
The Textile / Footwear industry, 69% of companies utilize this period of time to implement productivity improvement solutions to maintain market leadership.
-
64% of companies in the Pharmaceuticals / Biotechnology industry utilize this period of time to implement productivity enhancing solutions to maintain market leadership.
-
It is worth noting that 71% of companies in the Agriculture / Forestry industry use this period of time to implement productivity improvement solutions to maintain market leadership.
-
70% of companies in the Automotive / Automation industry utilize this period of time to implement solutions to improve productivity.
-
The High-tech industry, the Industrial Products industry, the Production of Construction Material industry and other industries do not have too large a ratio difference in the companies that choose to prepare for the market or ensure to maintain company operations.
For more details please refer to the report
2. Automation application
Most manufacturing companies promote automation, especially in the production stage.
All manufacturing industries tend to apply automation to production.
In detail:
-
In the High-tech industry, 52% of companies apply automation to all stages.
-
In the Textile / Footwear industry, 60% of companies apply automation to the production stage.
-
The Pharmaceuticals / Biotechnology industry has 62% of companies applying automation for production.
-
In the Agriculture / Forestry industry, 64% of companies apply automation to the production stage.
-
In the Industrial Products industry, 54% of companies apply automation to the production stage.
-
The Consumer Goods / Food Manufacturing industry has 50% of companies applying automation to the production stage.
-
The Production of Construction Materials industry has 52% of companies applying automation for production.
-
The Automation / Automotive industry has 82% of companies applying automation for production.
-
In the other industries, 75% of companies apply automation to all stages.
For more details please refer to the report
PART 3: RECOMMENDATIONS FROM VIETNAMWORKS
I. FOR COMPANIES
Recruit skilled personnel during the lay-off to catch the recovery wave
Companies choose the solution of downsizing, causing many employees to be cut. Taking advantage of this opportunity, enterprises are easier to filter and recruit skilled workers than before, contributing to strengthening internal resources and equipping elite teams in the future. From there, it is possible to gain momentum to catch up with the recovery signal from the market.
Build an effective recruitment strategy
With the current recession situation, making a recruitment plan to get good and highly specialized personnel while still meeting the company’s budget is the solution that every company needs. Therefore, companies should implement recruitment strategies that meet these criteria in order to build a strong team ready for the future. VietnamWorks always supports companies, especially during this difficult time with preferential recruitment packages and suitable financial resources. Thereby helping companies recruit effectively at a very reasonable cost. Please leave your contact information to learn more about related service packages from VietnamWorks.
II. FOR EMPLOYEES
Update knowledge and skills to adapt to automation
Most companies are applying automation to some or all sewing threads. Therefore, employees need to constantly update their knowledge and skills in order to be able to operate and control the machine. From then on, new employees can adapt and continue to develop in the industry.
Learn more essential skills
After experiencing COVID-19 twice and the economic crisis, we all saw the importance of developing skills to maintain work and career development. The following are the three most common skills that companies need from employees:
-
Effective communication
-
Technology and technical skills
-
Time management
Refer to and download the full Report on Human Resources in the Manufacturing Industry 2023 at:
– Vietnamese: bit.ly/44SlyDY
– English: bit.ly/47gldg9